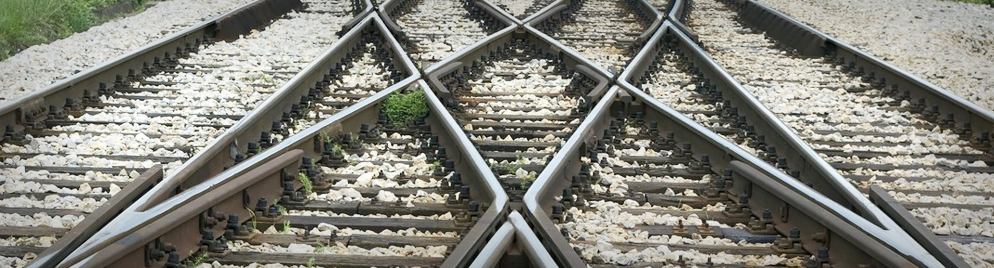
Quelles voies vers l’Industrie du Futur pour les procédés de transformation ?
La revue Nature publiait en avril dernier un article d’Andrew Kusiak intitulé « Smart-manufacturing must embrace Big Data » [1]. Professeur américain de mécanique et génie industriel, spécialiste des questions de big data, Kusiak analysait les freins rencontrés par les industriels dans l’intégration de ces nouvelles technologies et livrait son point de vue sur le rapport des entreprises à la donnée :
« Most companies do not know what to do with the data they have, let alone how to interpret them to improve their processes and products. […] Companies do not know what to measure or when. […] Manufacturers want to know what types of data to sample, which sensors to use and where along the production line to install them. »
Si le constat peut paraître sévère, il rappelle que la question des données dans l’Industrie du Futur recèle une dimension stratégique, invitant l’entreprise à s’interroger sur l’ensemble de la chaîne : Quoi mesurer ? Pour quelle raison ? Par quel moyen ? A quel moment ? Qu’en faire ?
Qu’en est-il de ces enjeux pour les procédés industriels de transformation, pour lesquels la question de la mesure est souvent loin d’être triviale?
Les procédés de transformation ou la question des changements d’état de la matière
La fabrication industrielle d’une crème dessert, d’un rouge à lèvre, d’une graisse lubrifiante, d’un revêtement de sol ou d’un composite de renfort automobile procède d’un même principe général : donner forme, structure et fonctionnalités à un produit par des moyens techniques de traitement et de transformation de matières formulées.
Broyage, mélange, pompage, transport, traitement thermique, injection, extrusion, enduction, pulvérisation, etc. Les poudres, solutions, pâtes se combinent, s’étirent, réagissent, s’écoulent, durcissent…
A chaque étape, certaines combinaisons de propriétés (chimiques, physiques, thermiques, mécaniques, rhéologiques, …) de cette matière en transformation sont mobilisées d’une façon spécifique aux conditions de l’opération unitaire, dont les réglages optimaux dépendent eux-mêmes de l’état de la matière entrante.
Ainsi, malgré le savoir-faire et l’ingéniosité des équipes, des altérations parfois minimes dans les proportions d’ingrédients, les conditions de préparation, le réglage des équipements ou la thermique du site peuvent provoquer des variabilités notables, voire des non-conformités des produits, que de nombreux industriels estiment « subir ».
Face à ces questions, l’Industrie du Futur – ou ses équivalents : Industrie 4.0 ou Smart-Manufacturing- n’échappe pas à la tendance actuelle d’une vision futuriste selon laquelle la machine résoudra tôt ou tard les problèmes à la place de l’Homme. Mais en attendant, comment procéder?
Quand la Data n’est pas donnée
S’appuyant sur son expérience dans les domaines de l’énergie, de l’aéronautique ou des semi-conducteurs, Kusiak identifie dans son article cinq Data gaps à franchir pour mettre en place un véritable Smart-manufacturing :
- Adopter une stratégie de la Data
- Optimiser la collecte des données, leur utilisation et leur partage
- Concevoir des modèles prédictifs
- Etudier des modèles prédictifs généraux
- Connecter les usines aux procédés de contrôle.
Kusiak précise notamment l’approche de la première étape : « […] At first, sensors would monitor the states of existing equipment. As new needs for quality and efficiency emerge, more sensors can be added to follow the most useful parameters. […] ».
Dans les procédés de transformation, la température d’une cuve ou la pression en différents points des conduites correspondent en effet à des quantitités d’intérêt mesurables par un capteur.
Mais quid des cas où la quantité d’intérêt n’est pas mesurable en ligne – ce qui est le cas pour un certain nombre de propriétés notamment physiques impactant les comportements en process : granulométrie d’une poudre, profil rhéologique d’une pâte, tension de surface d’une suspension, … ?
Autre complexité : le « paramètre représentatif »d’un phénomène ou d’un effet peut être une combinaison, plus ou moins complexe, de certaines quantités mesurables.
Dans ces cas de figure, les étapes de modélisation prédictive suggérées par Kusiak sont susceptibles d’impliquer une analyse combinée de données en-ligne et hors-ligne, faisant au passage disparaître une certaine forme de « temps-réel » avec la nécessité de quantifier certaines données en différé. La question de la connexion des usines aux procédés de contrôle prend alors un sens différent d’une pure automatisation.
Une telle analyse des procédés de transformation, pour sommaire qu’elle soit, donne ainsi à apercevoir un « angle mort » de l’Industrie du Futur : les approches Data-based présupposent souvent que les données d’intérêt sont non seulement identifiées mais qu’elles font (ou peuvent faire) l’objet d’une quantification par capteur ou dispositif de mesure en ligne, autorisant ainsi un recueil automatique, à distance, massif et temps-réel de données pour alimenter des boucles de rétroaction instantanées.
Que faire lorsque ce n’est pas le cas ? S’agit-il de renoncer à la puissance du Big-Data, de l’Intelligence Artificielle ou de l’Internet des Objets ?
Pour une stratégie de la Mesure
Dans ces contextes où les technologies 4.0 ne sont pas directement « prêtes-à-l’emploi », une stratégie de la Data nécessite une stratégie préalable de la Mesure pour déterminer les données mesurables d’intérêt et les techniques de mesure associées.
Les données d’intérêt peuvent être les paramètres quantifiant en sortie de production la non-conformité réelle des produits -au regard des attentes clients, pas seulement du contrôle qualité- ou les paramètres représentatifs des états de la matière en cours de transformation ou attendus à l’issue d’une étape process avant le passage à la suivante.
En pratique, c’est l’étude de la corrélation des variabilités de quantités mesurables représentatives aux différents facteurs d’influence du procédé ou de l’application qui détermine les paramètres discriminants. Et fixe donc les techniques instrumentales appropriées .
Une véritable stratégie de la Mesure se construit donc dans ce double mouvement de compréhension opérationnelle des facteurs d’influence des phénomènes et de mise sous contrôle par l’identification des paramètres représentatifs et des techniques de mesure appropriées ainsi que l’ébauche de modèles de corrélations –prédictifs par construction.
Une stratégie de la Data en pleine conscience semble alors envisageable, dans un premier temps pour évaluer la possibilité ou non d’un contrôle complet du process par des mesures en ligne et orienter le choix -ou le développement- des techniques de mesure adéquates.
Pour les procédés de transformation nécessitant le couplage d’approches en-ligne et hors-ligne, les technologies de la mesure, du numérique et du traitement de données ouvrent la voie au développement de stratégies complémentaires et convergentes entre R&D et production, certainement à même de contribuer à la fluidité et la souplesse préconisées par les programmes de l’Industrie du Futur pour gagner en compétitivité.
L’équipe RHEONIS
[1] http://www.nature.com/news/smart-manufacturing-must-embrace-big-data-1.21760
NB. Cet article ayant pour vocation d’alimenter la réflexion, le débat et l’échange, n’hésitez pas à partager de vos commentaires, remarques, questions ou à nous contacter en message-privé pour toute discussion.
Last Updated on 2 septembre 2019 by Vincent Billot